Boat Building Design & Culture
Shop and teaching assistant for ENGN 0860/AMST 1220: Boat Building Design & Culture at Brown University. Construction of a 16-foot Peapod dory.
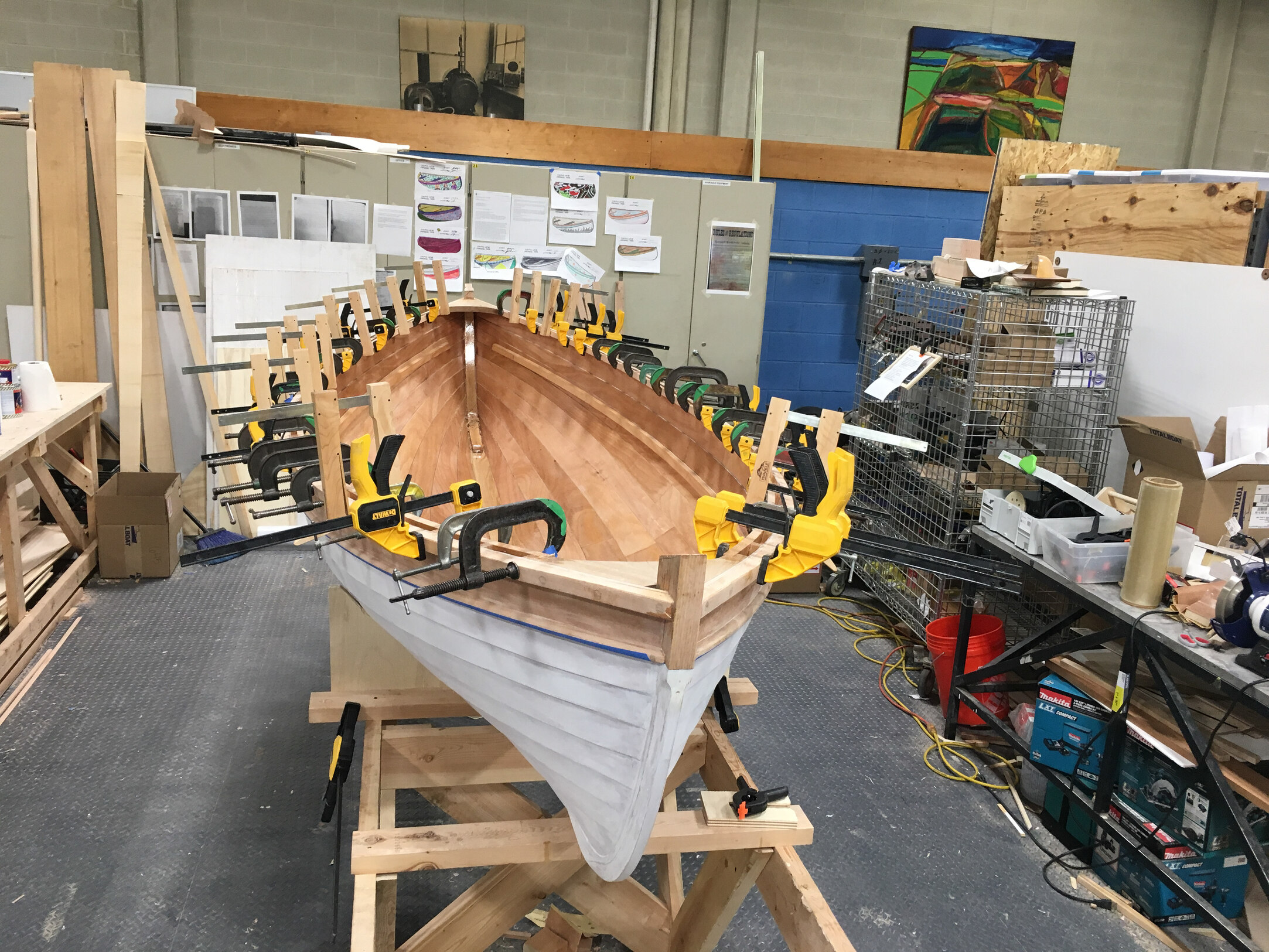
Background
The course was created after an introduction I made between one of my professors in American Studies, Steve Lubar, and a boat-builder, Shep Shapiro. I had helped Shep with one of his boat building projects, and was integrating boat construction techniques into my own work, such as the Boatrobe, since the Fall of 2017. This new course allowed me to build a small dory from scratch, side by side with a boat-builder. The course was co-taught by Steve, Shep and Prof. Chris Bull, director of the Brown Design Workshop. I led two of the lab sections, facilitated discussions in class, and worked alongside Shep after hours building many aspects of the boat to make sure we stayed on schedule. It was the first hands-on, collaborative course in the Brown Design Workshop.
Process
I guided students in groups of four to create their own full-size lofting on a sheet of plywood. Lofting involves drawing a set of two-dimensional lines in three different views to describe the hull in three dimensions.
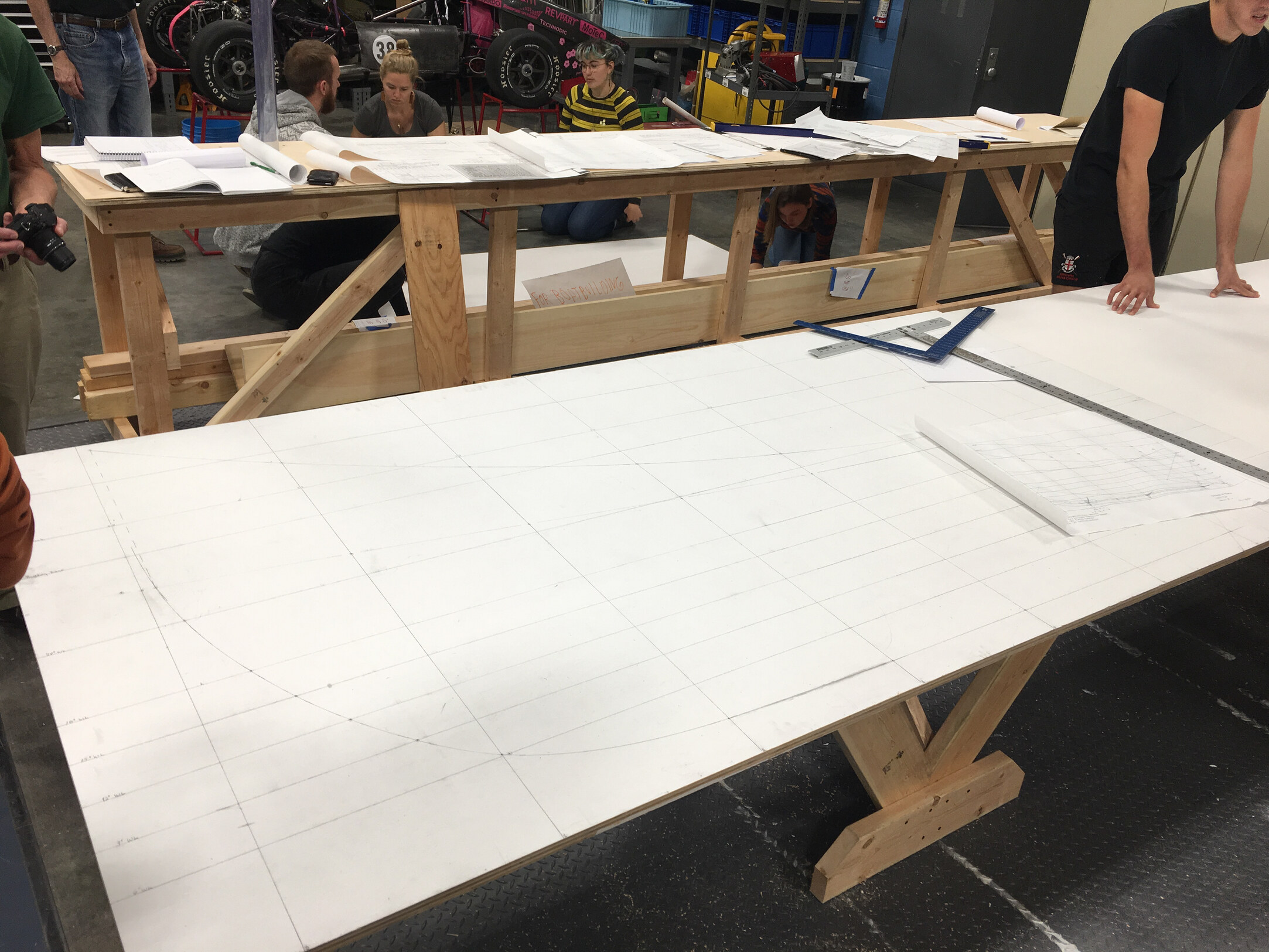
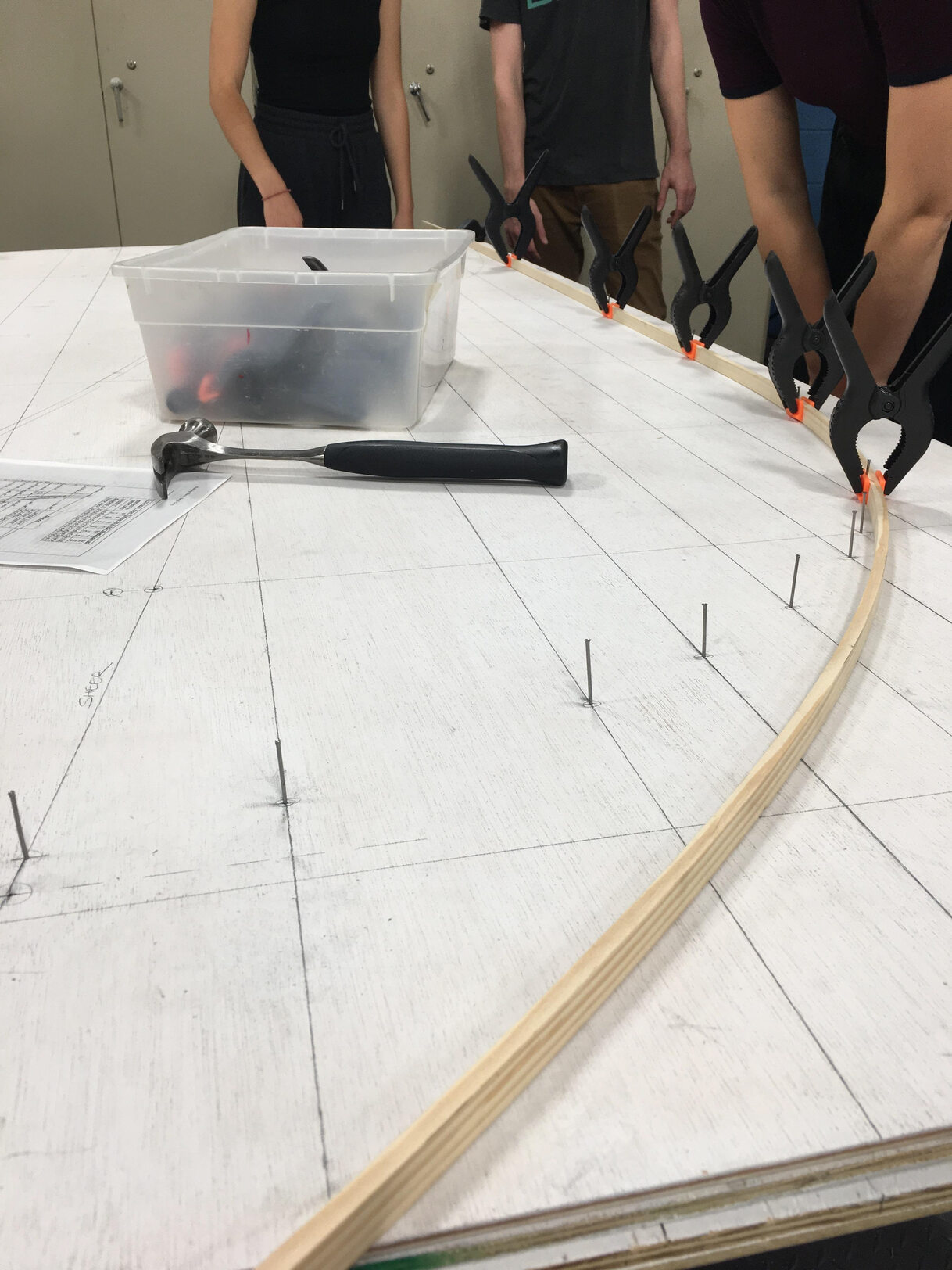
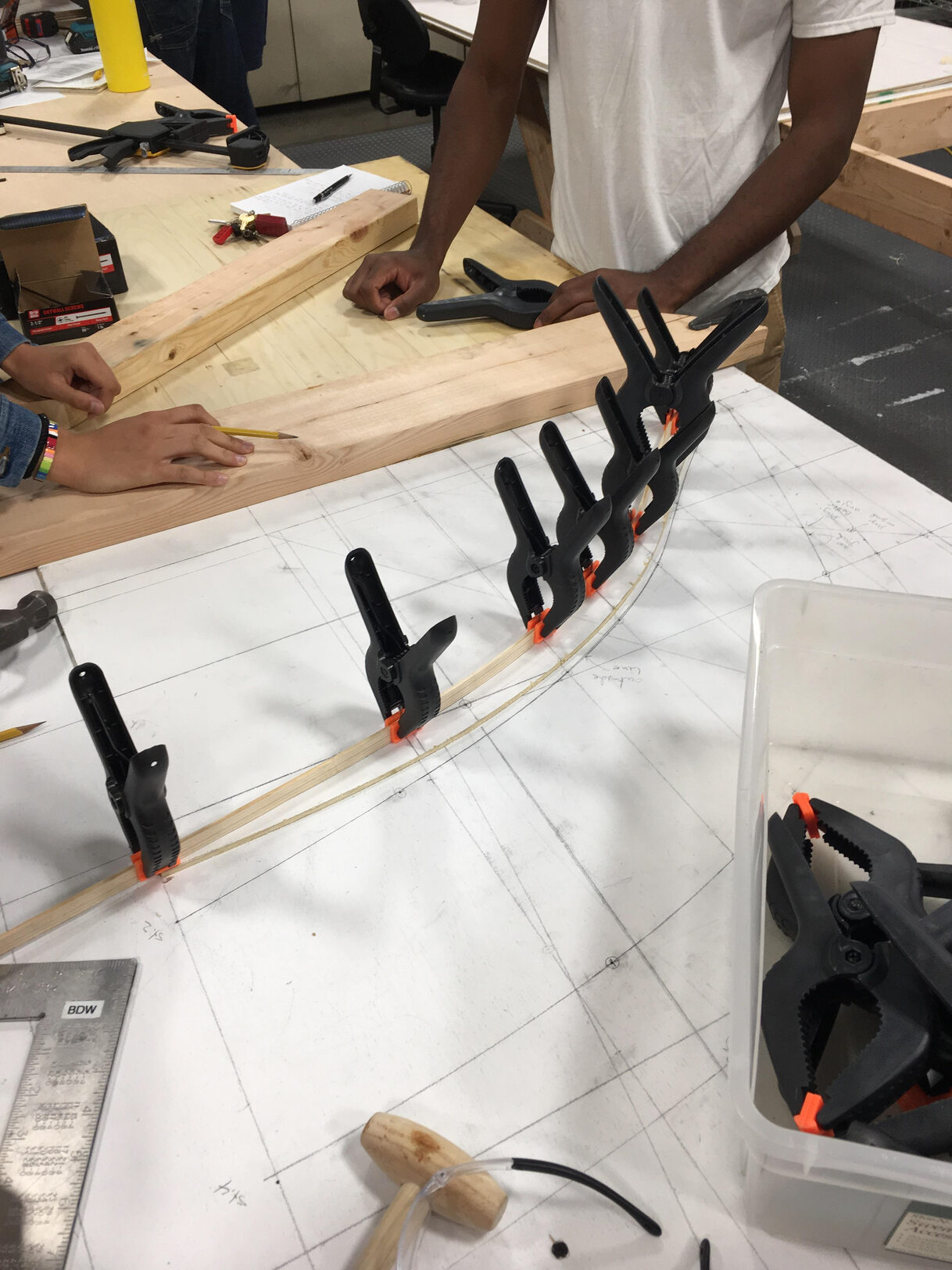
We used the full-sized lofting as a mold to laminate the inner and outer stems of the boat. The stems are where the planks join at the stern and bow of the boat, forming a rabbet joint. I taught each student to chisel and plane these rabbet joints by hand.
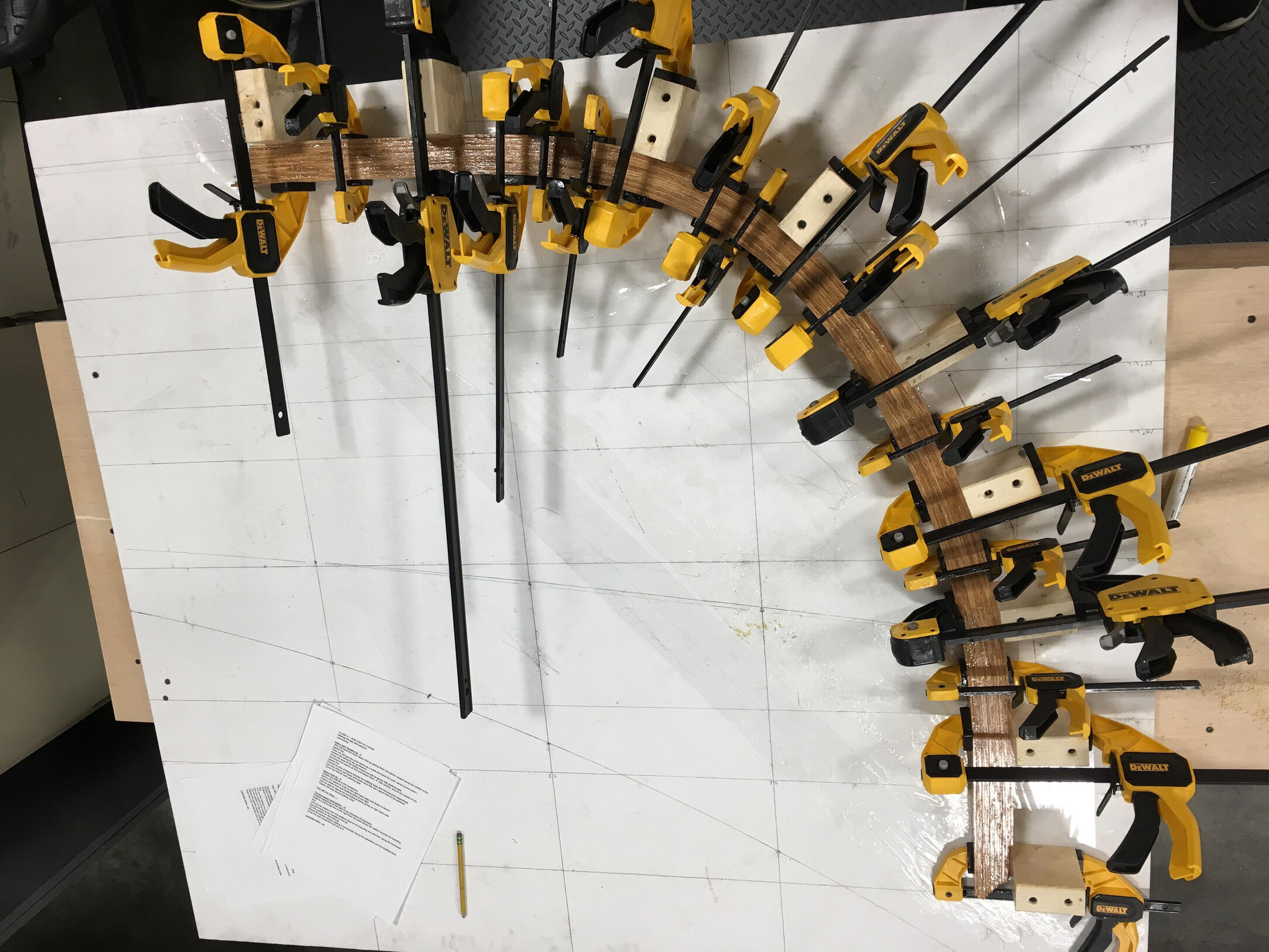
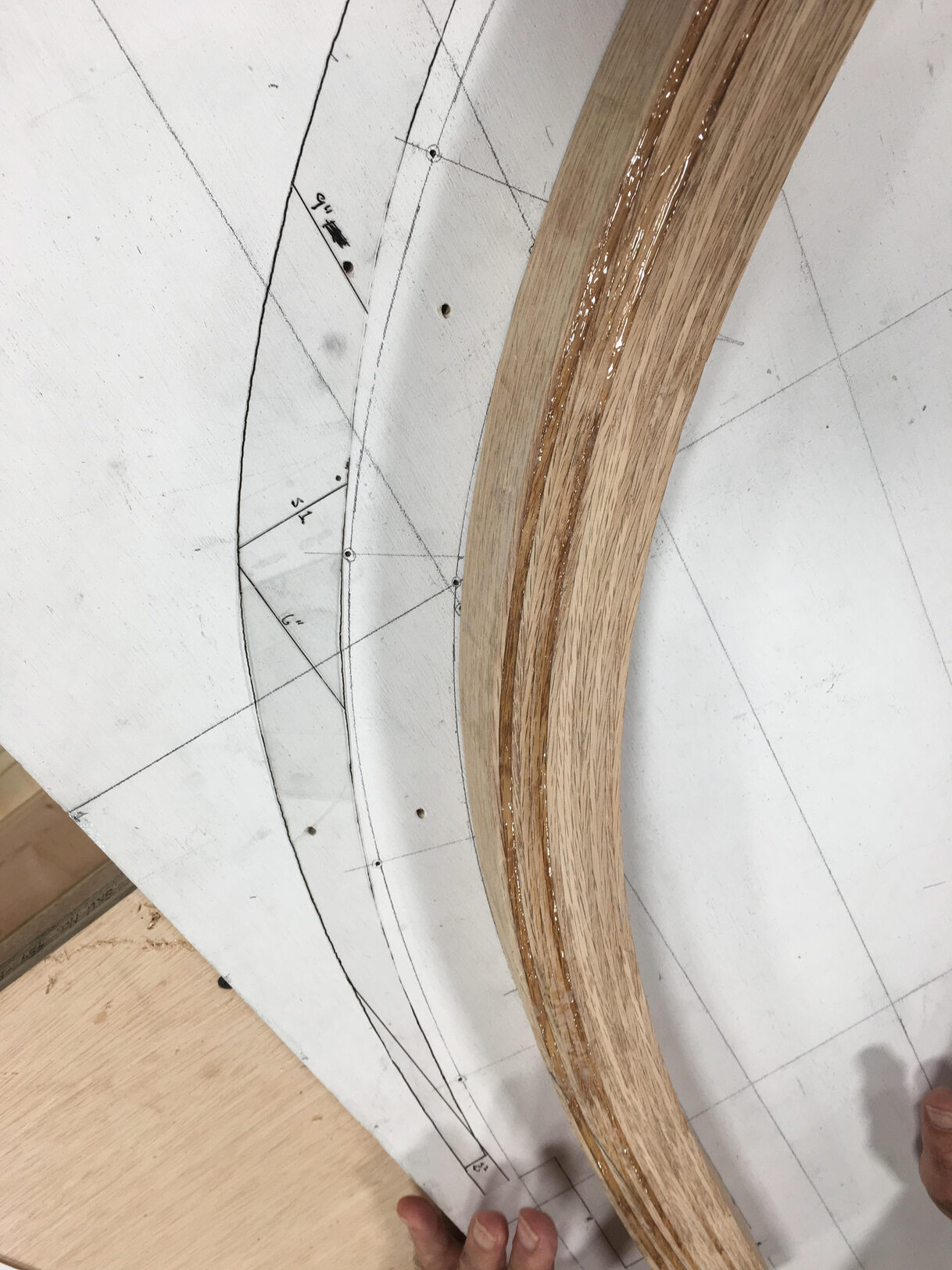
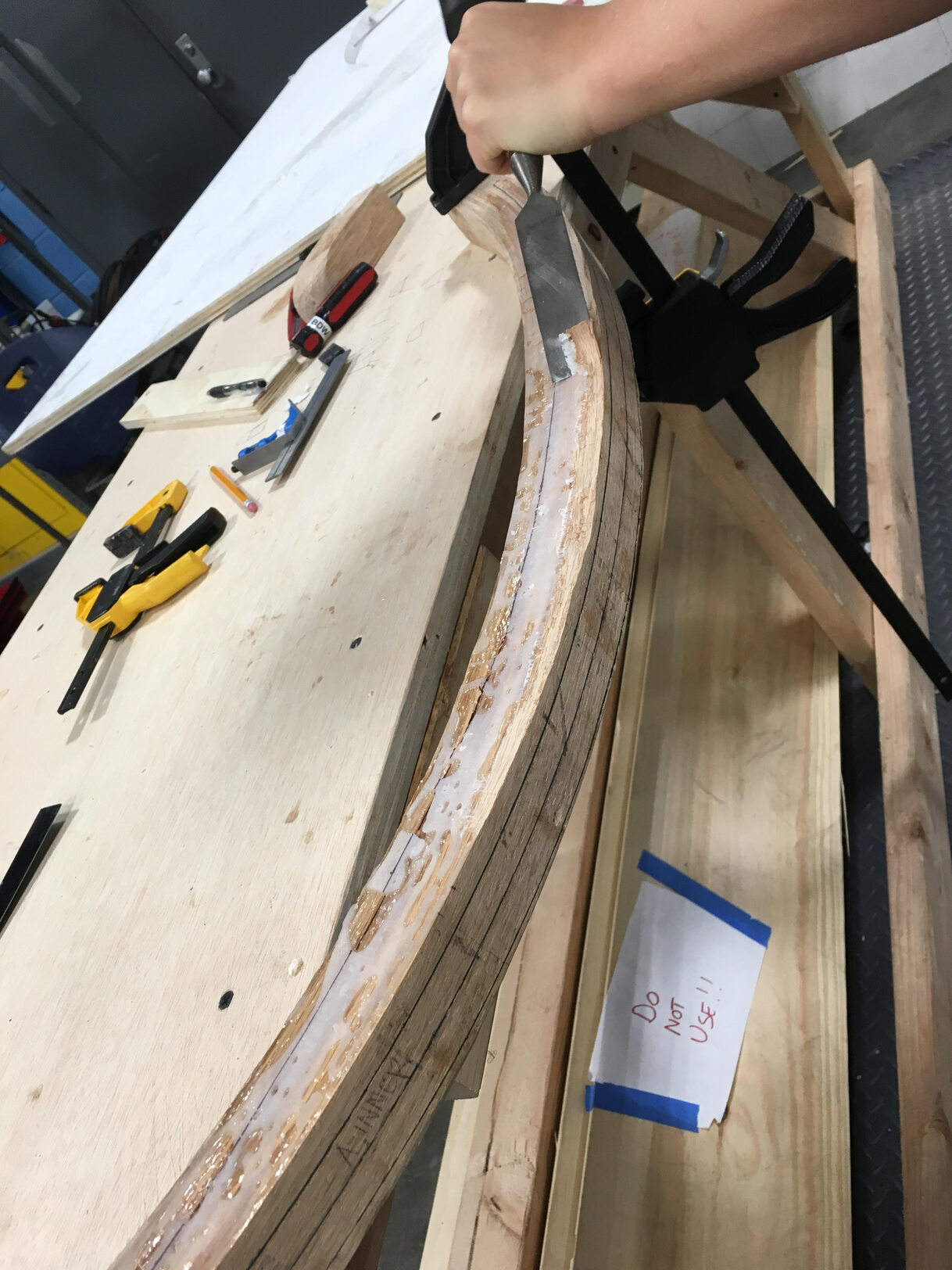
We also used the lofting to build stations, six sections slicing the boat at different hull widths. These are not part of the final boat, but serve as a mold. Combined, the two dimensional stations form a three dimensional mold that describes the complex curving planes.
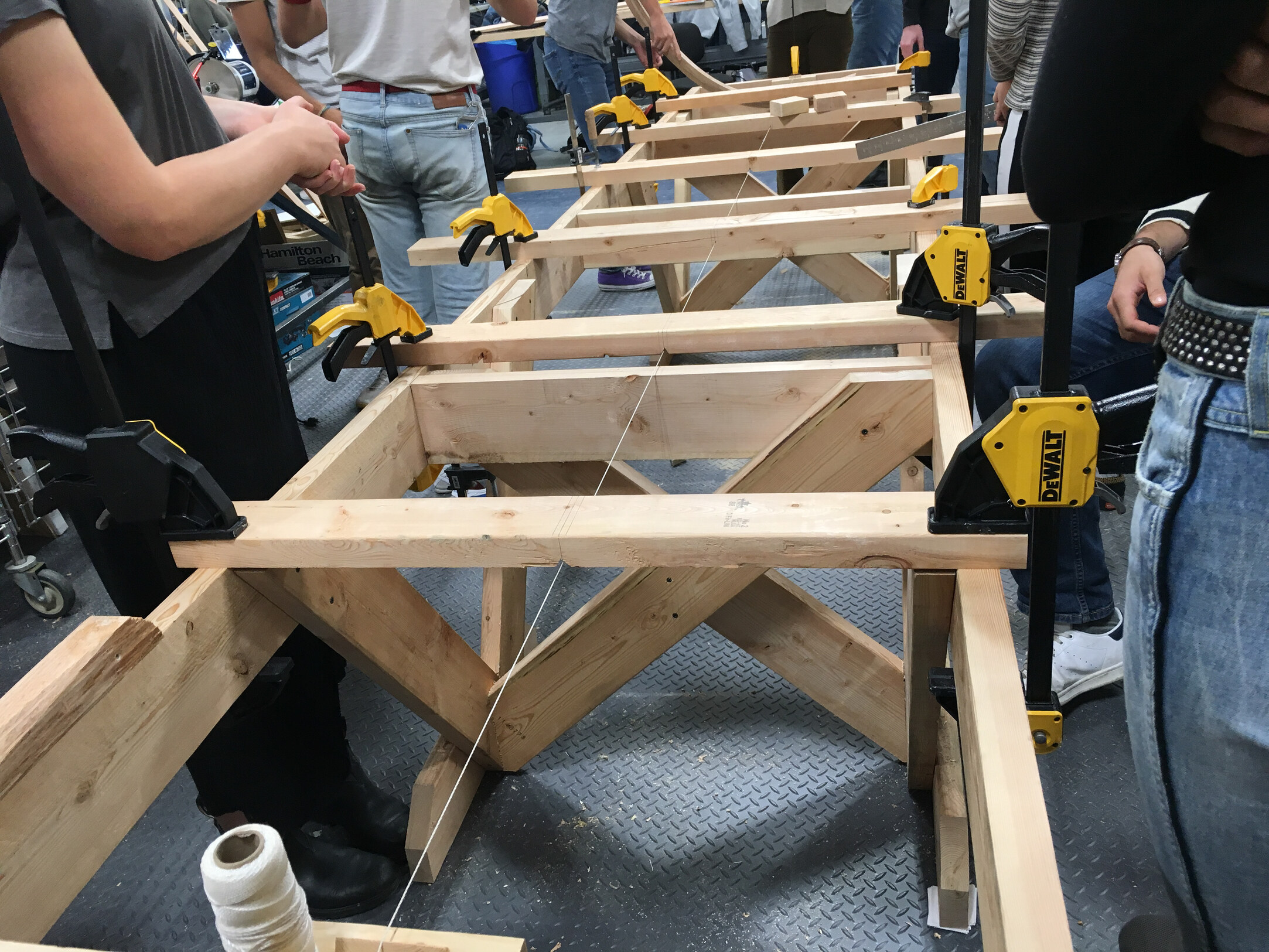
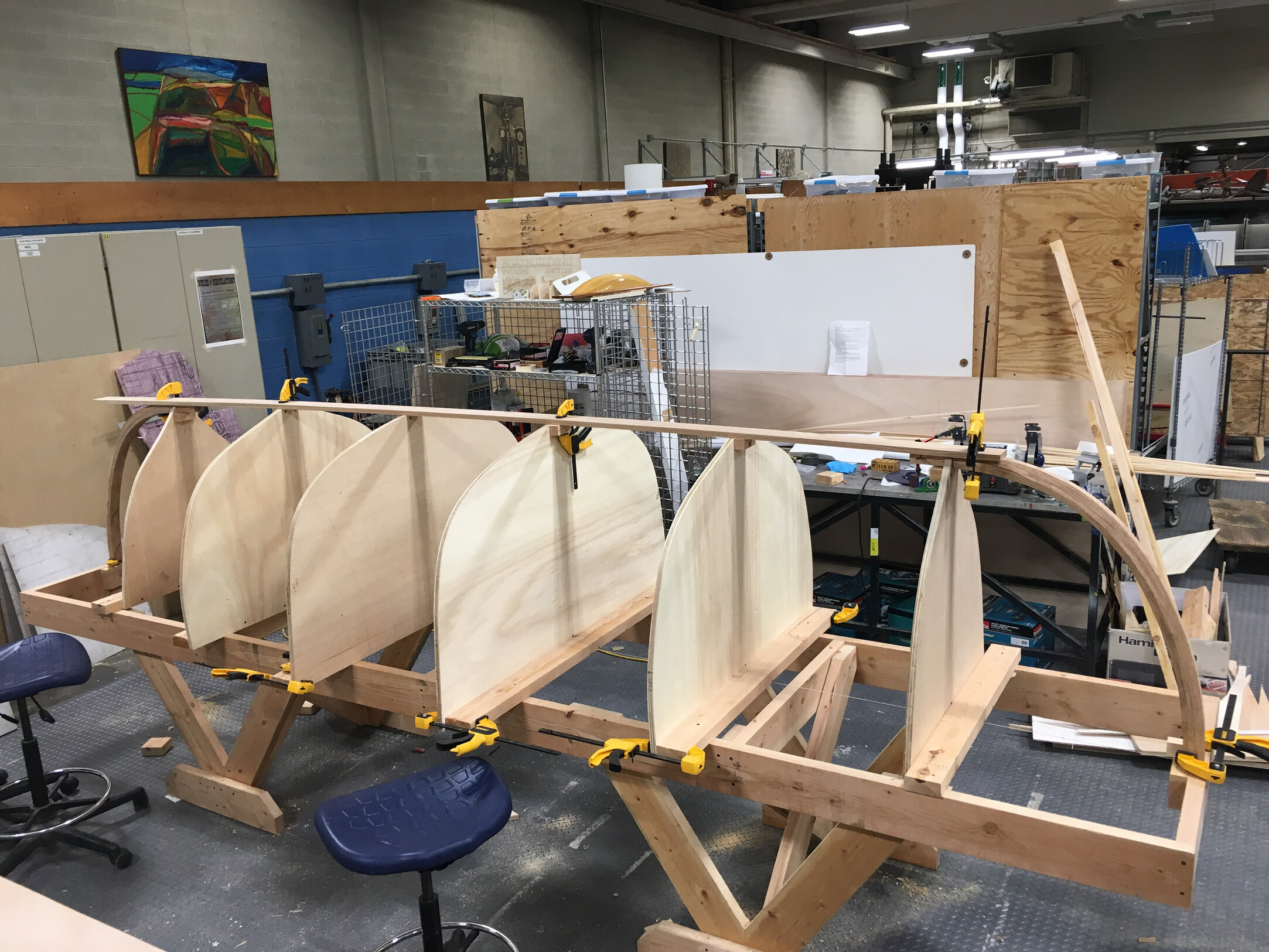
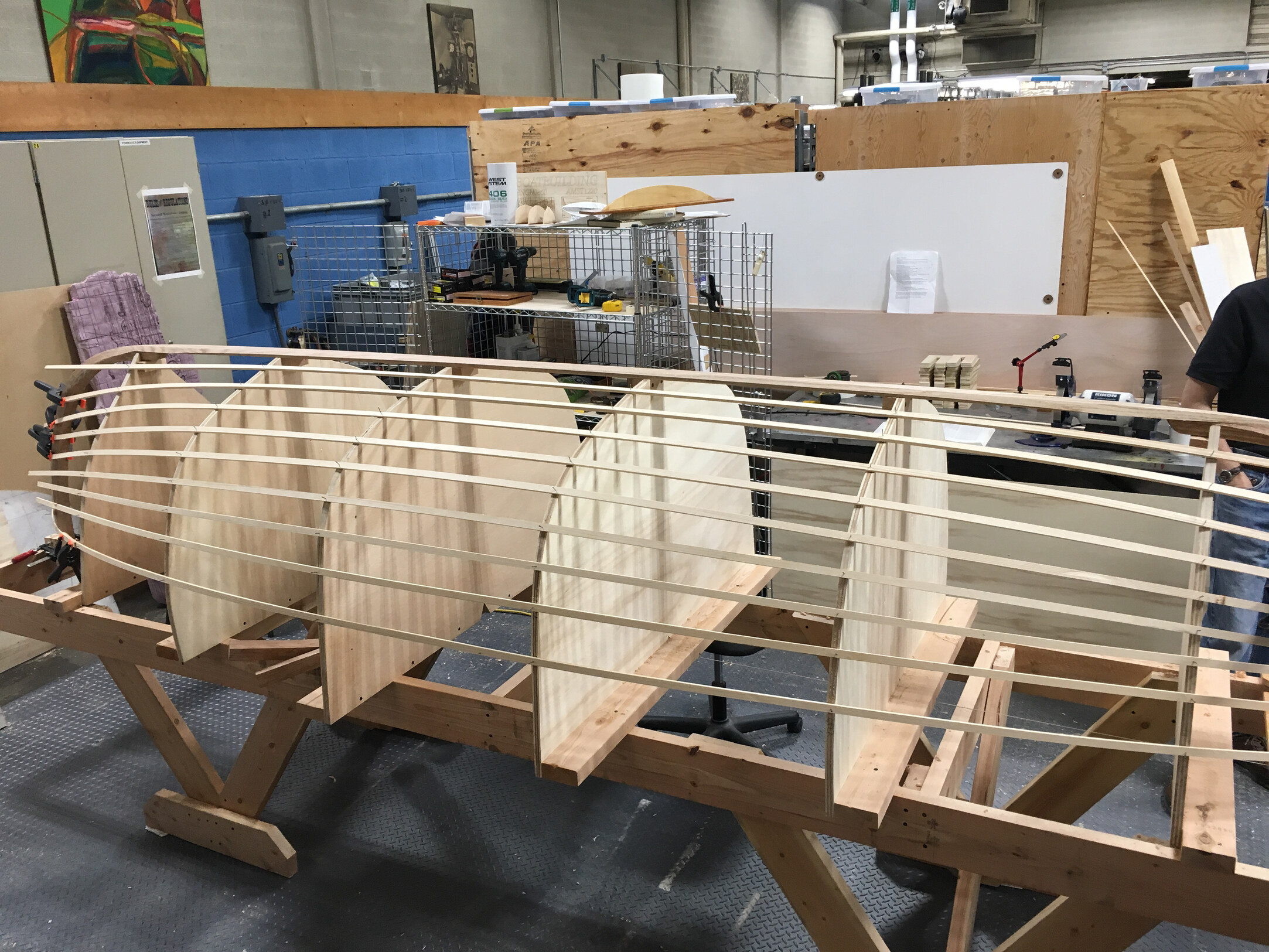
To determine the width of each plank, we used thin pieces of straight pine called battens. The battens allowed us to visualize the planks and create "fair" curves with no irregularities.
Next, I led two sections to plank the hull using 1/4 inch marine plywood. We made at least 40 specialized clamps to glue the planks evenly along their entire length. This process had to be done in two weeks, so I also traced, cut and glued planks on my own to stay on schedule.
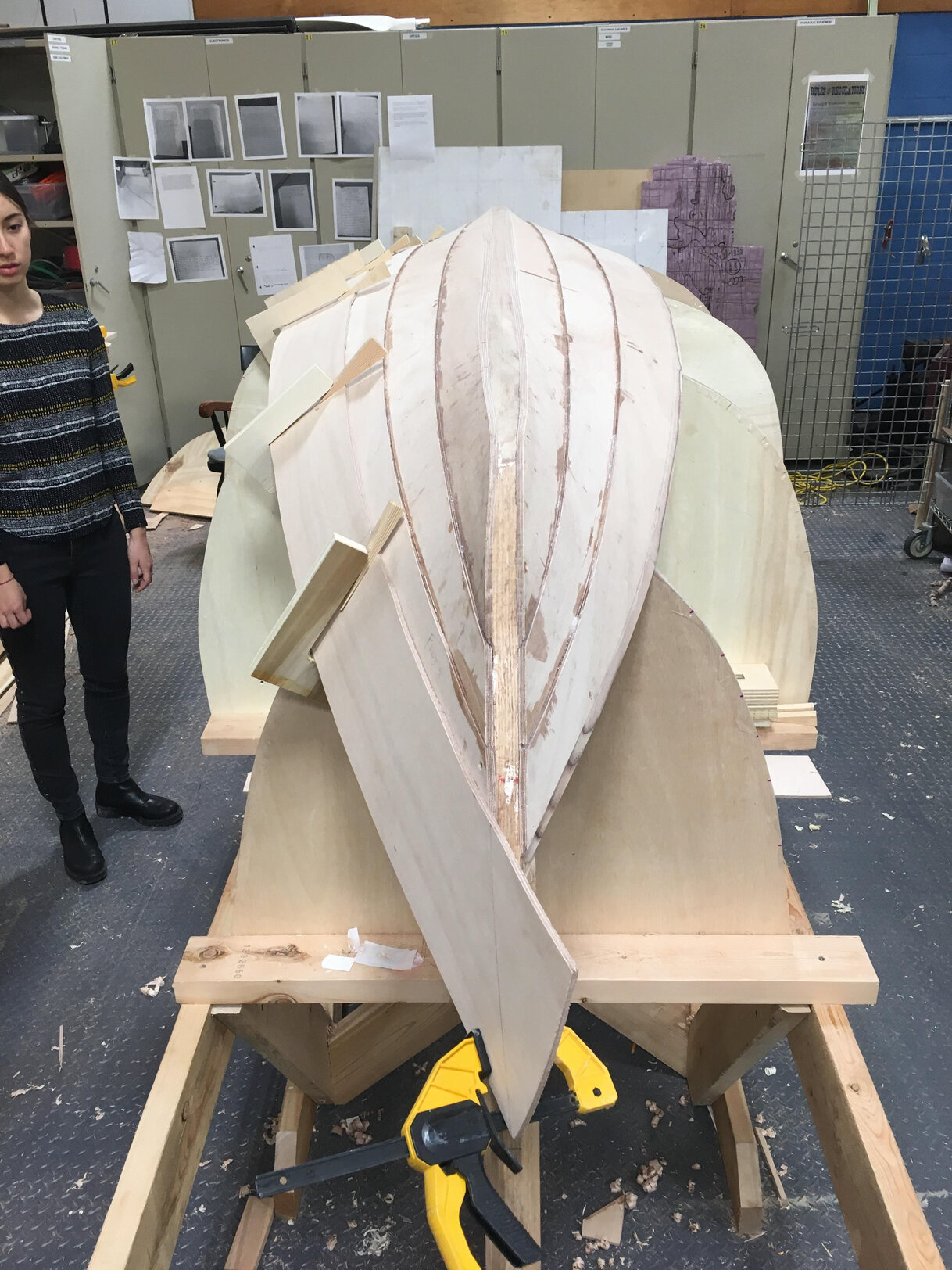
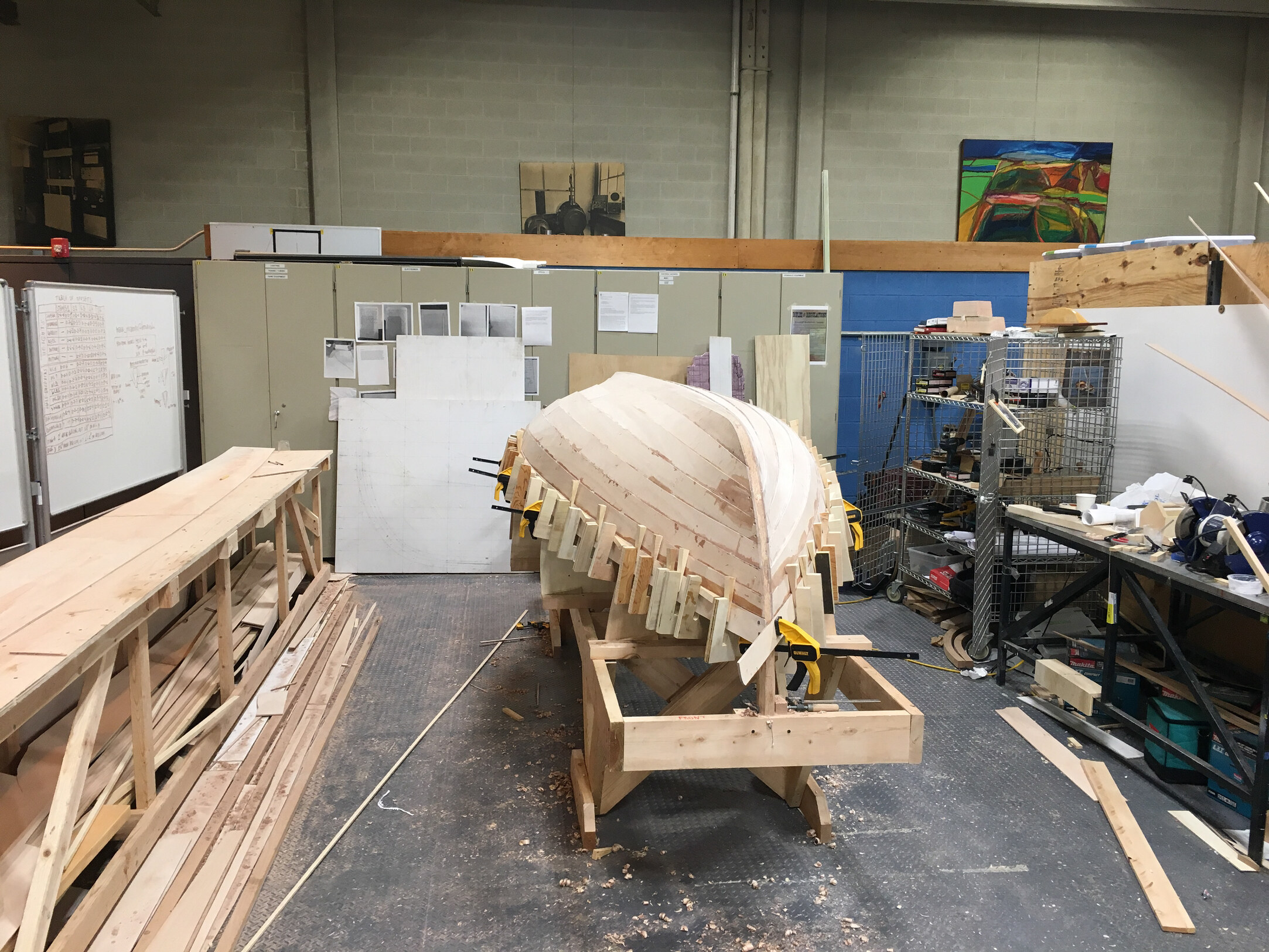
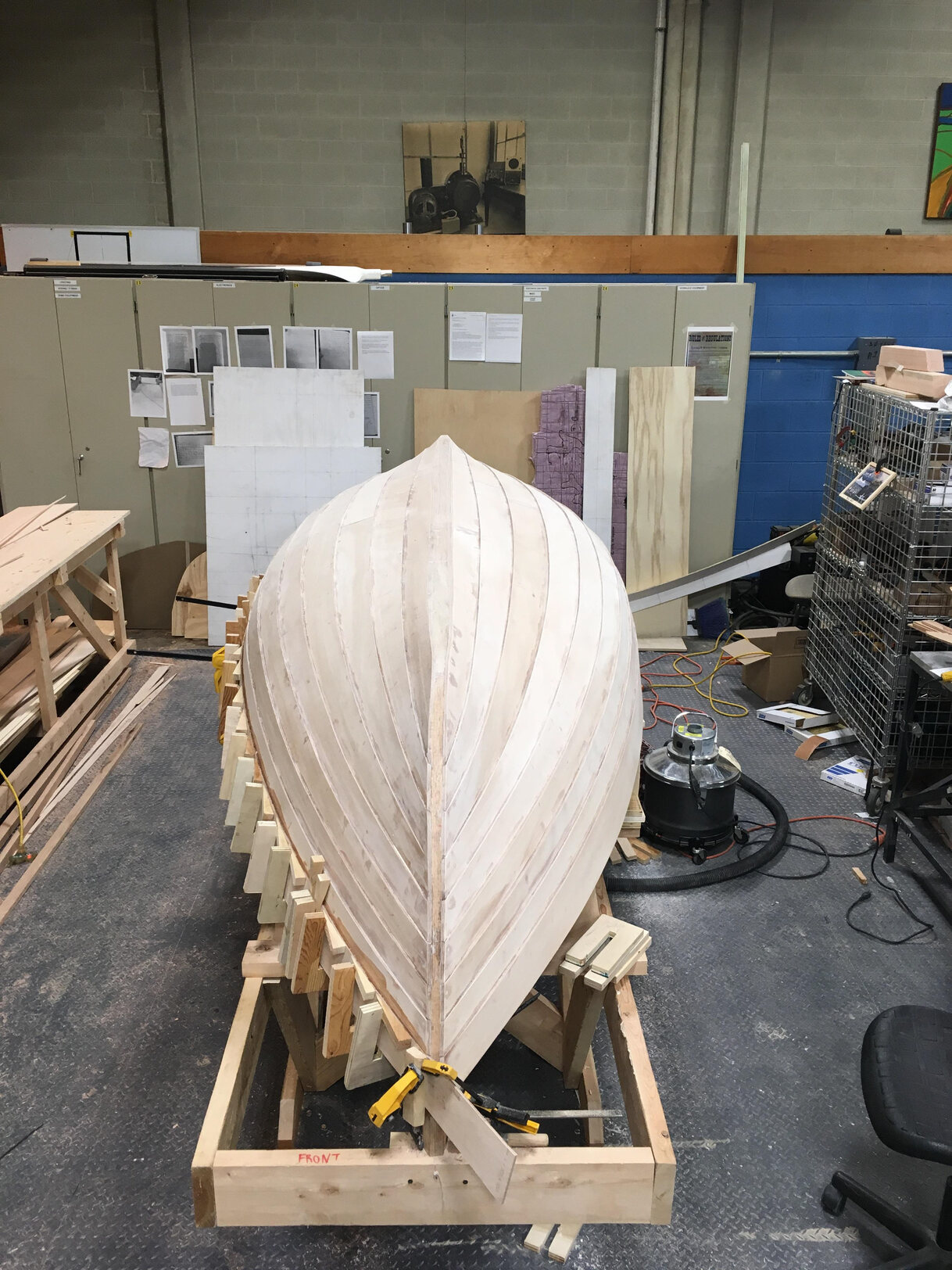
During the final week, I worked alongside Shep to make and glue the outer keel and gunwales.
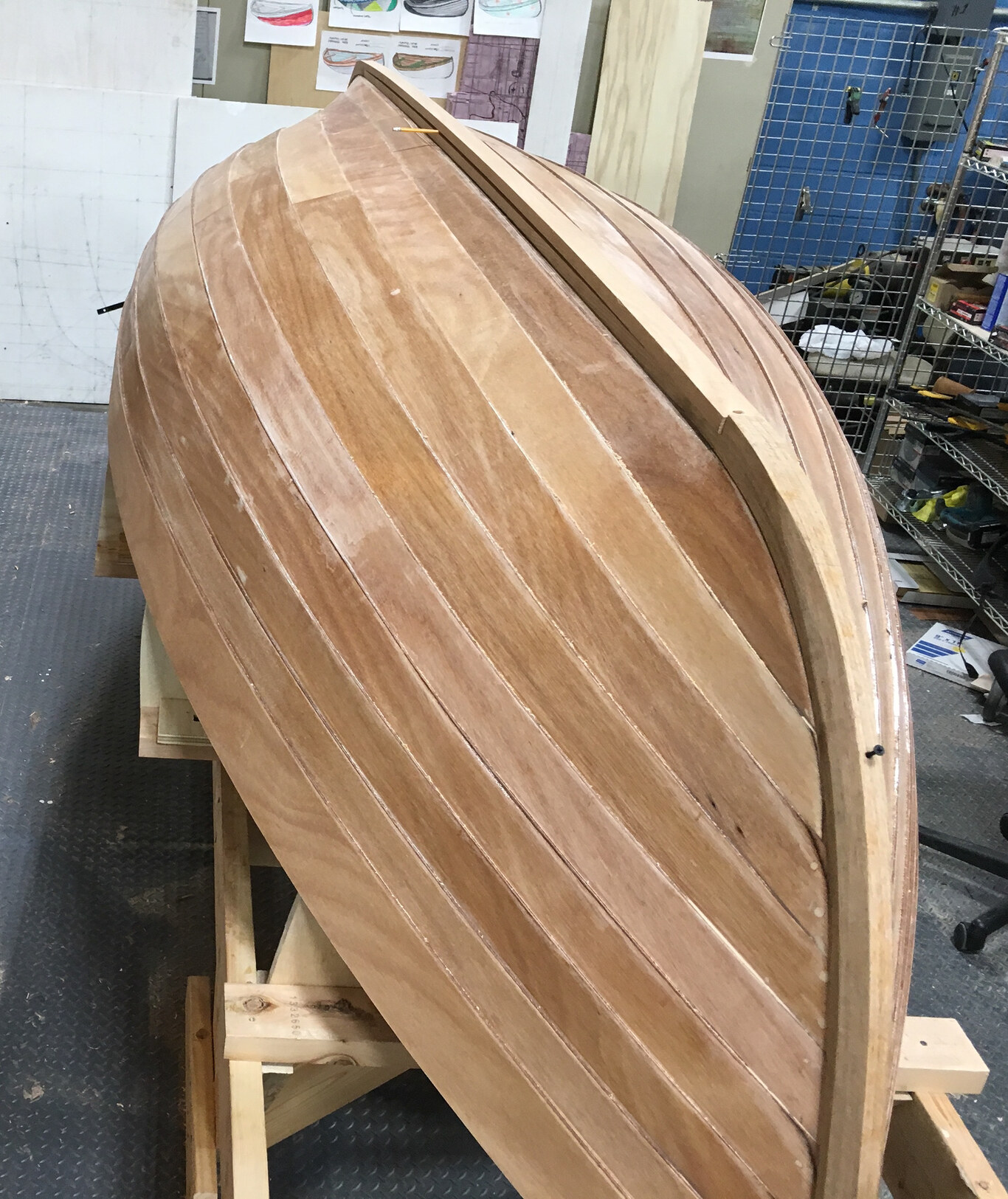
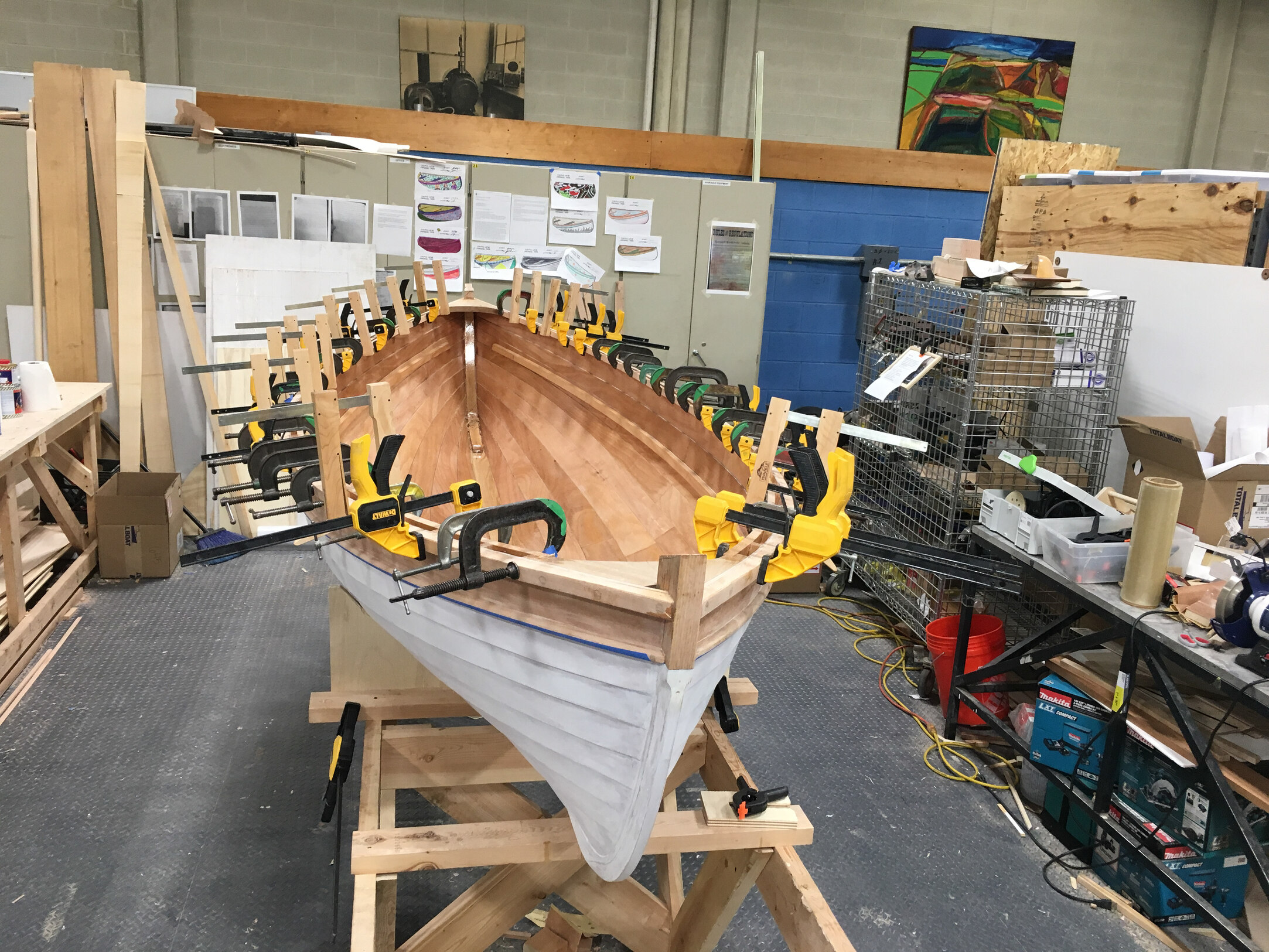
We then put the final coats of paint on, and installed the oarlocks and thwarts inside the boat. I mentored some students who wanted to build one of these parts as a final project.
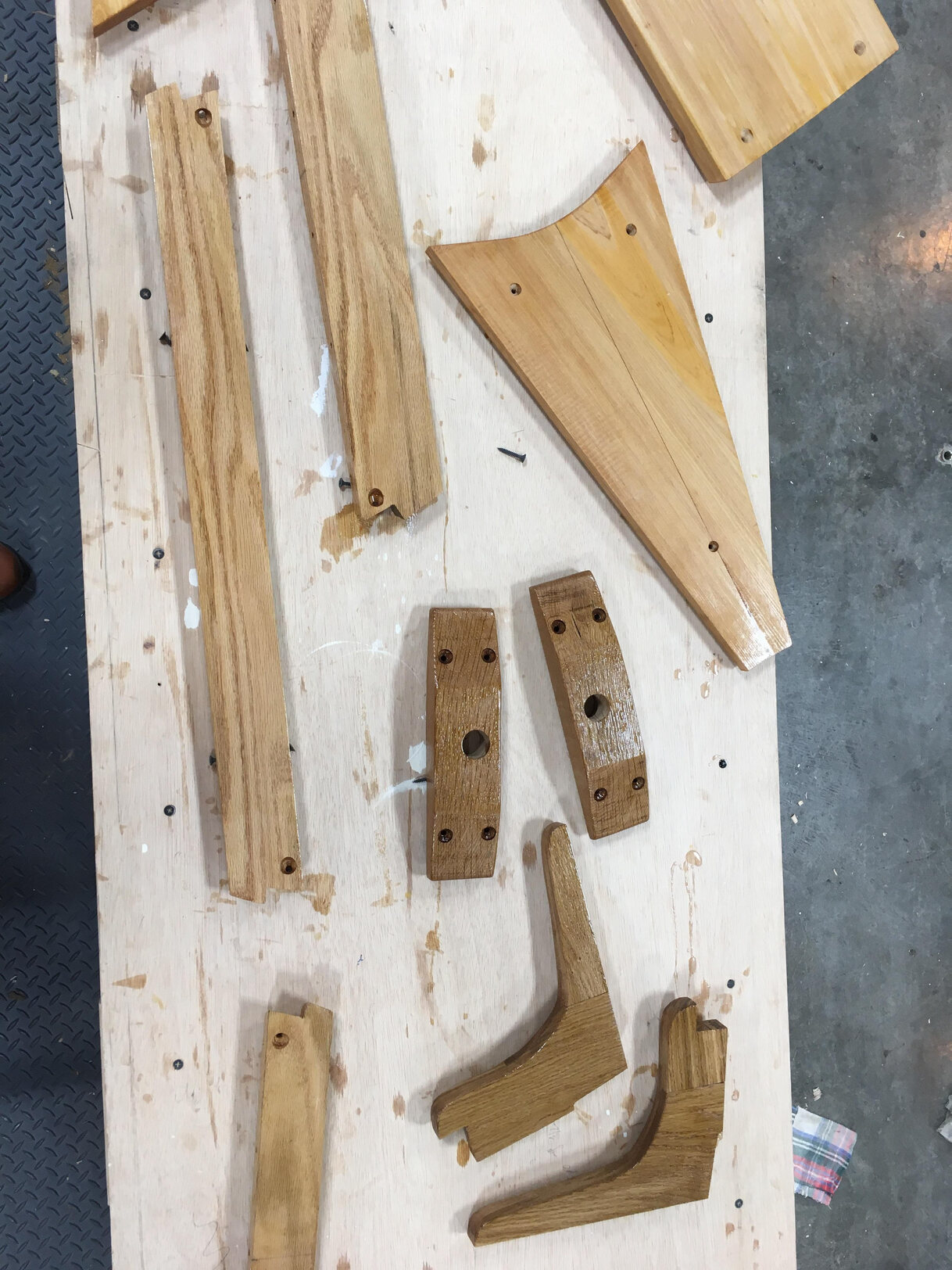
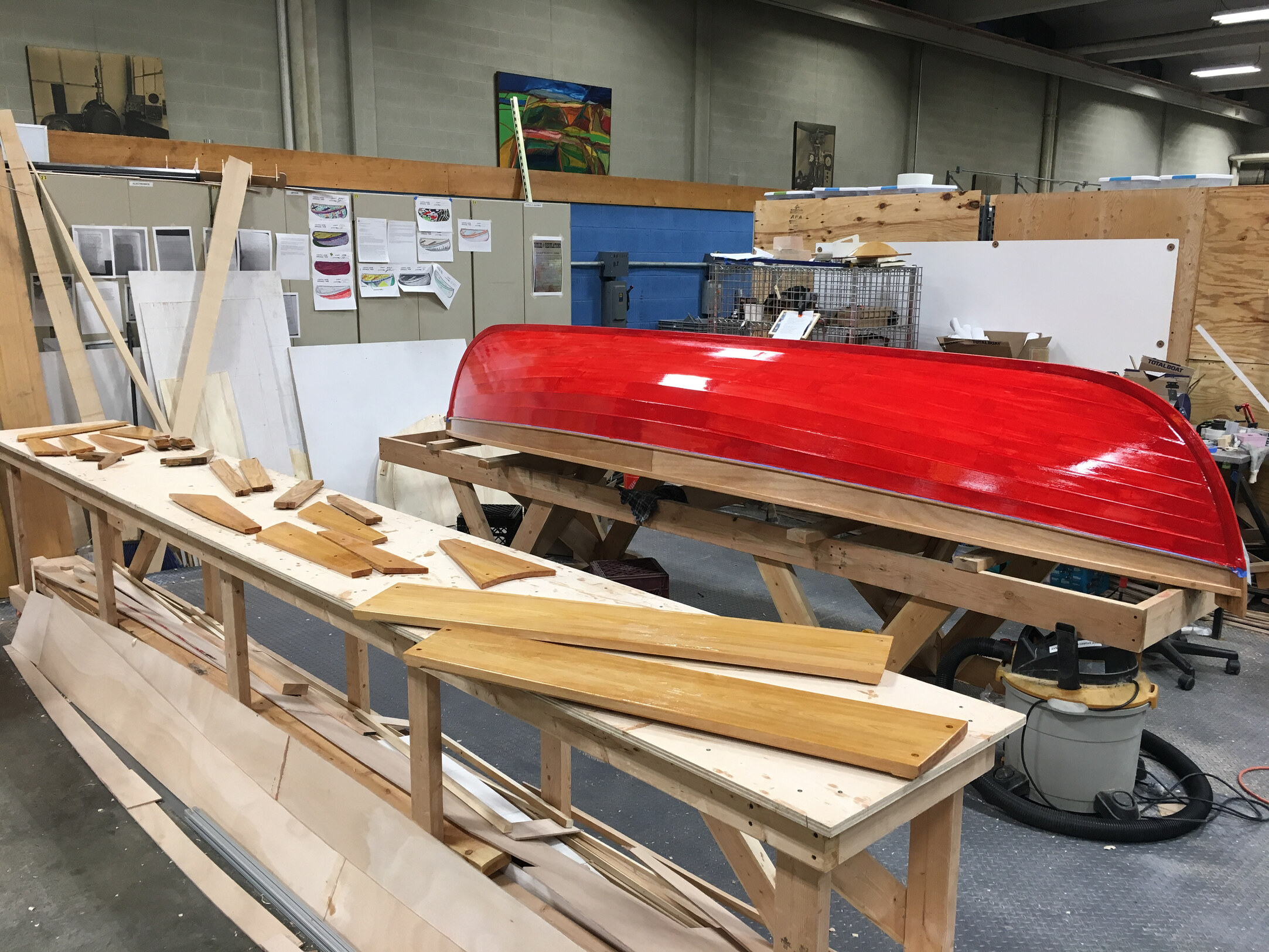
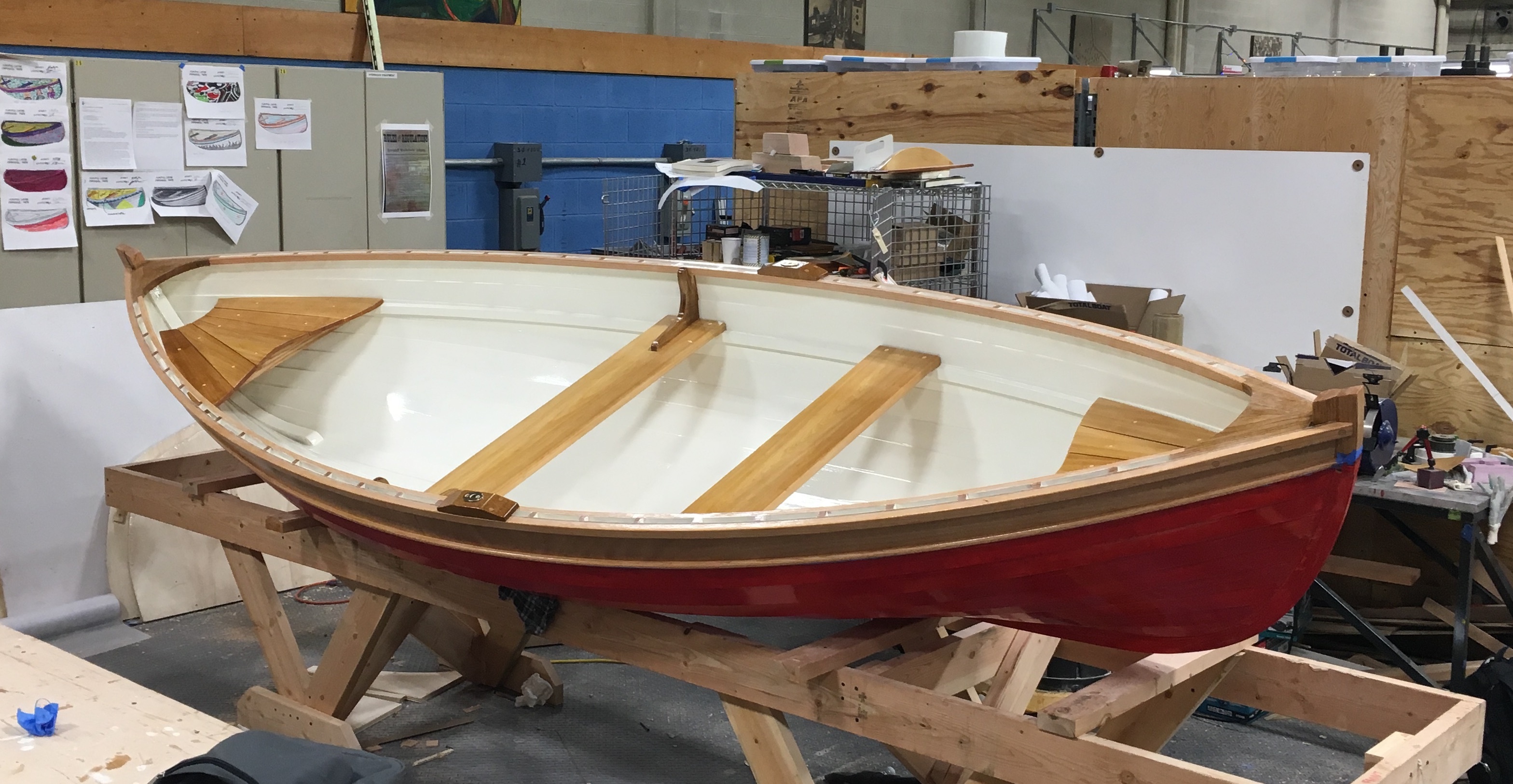
Launch
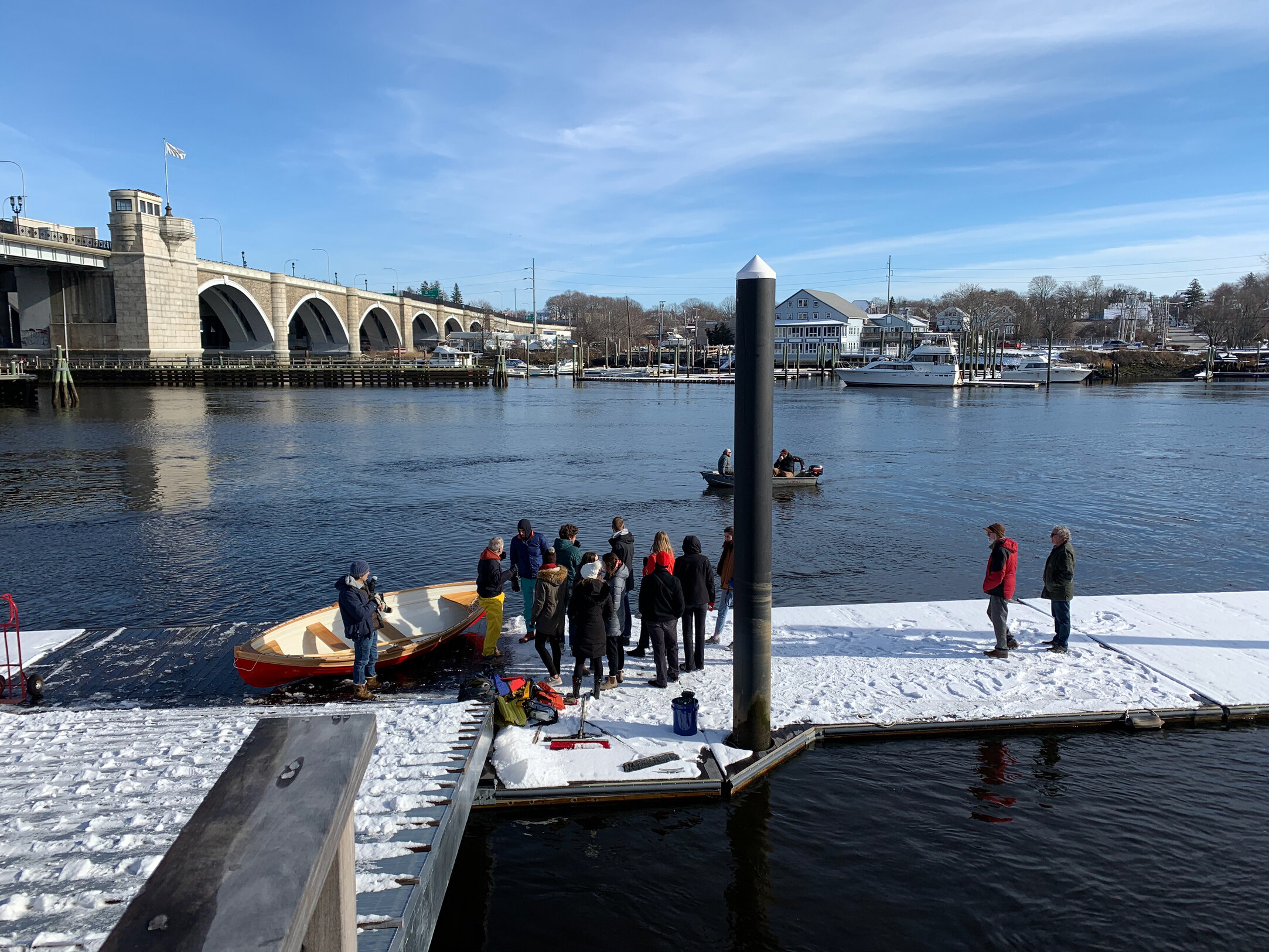